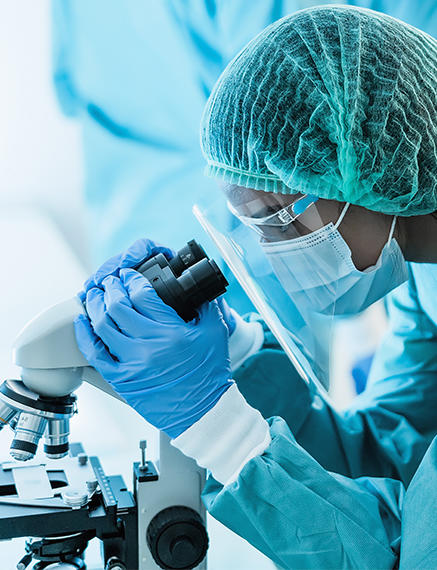
A global healthcare leader with an expansive portfolio of diabetes, oncology, immunology, and neuroscience medicines trusted Veolia Water Technologies to support the discovery and development of antibody therapies with a low-energy, high-purity water generation system that positions a modern central New Jersey facility to become carbon neutral.
Monoclonal antibodies (mAbs), engineered proteins that attack cancer cells like human antibodies in the immune system, revolutionized oncology care 30 years ago. Today, these “targeted therapies”, which have expanded into the treatment of multiple types of cancers and a variety of autoimmune/inflammatory diseases, represent more than two-thirds of biopharma sales and are the fastest-growing class of drugs.
Given this demand backdrop driven by the need of patients to enhance their immune systems against both oncological and non-oncological diseases, global biopharmaceutical companies are racing to accelerate their antibody pipelines through investments in antibody discovery and development. To this end, clinical and product development teams use water-intensive culturing processes in which cells grow suspended in aqueous solutions. Because cell culture can be highly sensitive to bacterial contamination, the use of high-quality water is paramount. While removing water impurities such as organics and microbial contaminants has routinely been the norm to maintain sterility, other molecules such as endotoxins, components of the outer shell of most gram-negative bacteria, can also affect the growth of cultured cells. These adverse responses are best avoided by ensuring the preparation of reagents with high-purity, endotoxin-free water.
Therefore, when low-bacteria and endotoxin-free water for injection (WFI) is used in the preparation of process reagents such as culture media and buffer solutions, end-to-end sterility is guaranteed from cell culture harvest through to protein isolation and purification. Furthermore, nonpyrogenic media also ensures high product yield peak cell density and maximum cell mass.

Figure 1: Specifications of water typically employed in the recovery of an antibody from mammalian cell culture at both laboratory and process-scale production
Main Parameters for ASTM D-1193 Type II water | |
---|---|
Conductivity (maximum) | 1.0 μS/cm at 77oF |
Resistivity (maximum) | 1.0 Mohms/cm at 77oF |
Total Silica | 3 μg/L |
TOC (ppb) | 50 |
Sodium (ppb) | 5 |
Additional Parameters for USP Water for Injection (WFI) |
|
Endotoxin Units (EU) | 0.25 |
Maximum Heterotrophic Bacterial Count | CFU, 10/100 mL |
Environmental responsibility and net-zero goals
Used in many process unit operations such as bioreactors and chromatography skids, WFI has been typically produced on-site through distillation techniques. This requires significant energy inputs because of the utility steam used in the heating process. As utility steam is generated in natural gas-fired steam boilers, the WFI-related carbon intensity is significant and the share of its emissions typically accounts for nearly a quarter and up to half of the total emissions of biopharmaceutical facilities.
The convergence of these high-purity water needs with the rapid industry growth translates into higher energy demands that result in an even higher environmental burden. This has serious implications for achieving carbon neutrality (Scope 1 and 2 emissions) since steam production represents the lion’s share of a facility’s fossil-fuel emissions. Thus, the need for optimizing WFI-production processes with improved energy efficiency that can cope with the increased quality and quantity demand while reducing emissions and phasing out fossil-fuel infrastructure whenever possible.
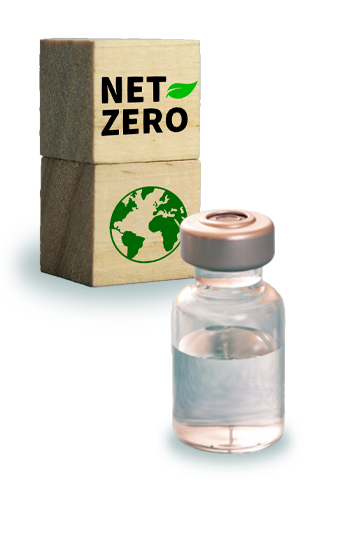
Project Case Study: Commercial and late-stage clinical manufacturing of recombinant mammalian therapeutics
Understanding this need, a project team working to develop a laboratory in the heart of central NJ favored robust but cost-effective sterile water purification solutions that are electrically driven. This made membrane WFI systems at ambient temperature the natural choice as they can be powered by low or zero-carbon electricity instead of carbon-intensive fuels. Beyond energy savings and building decarbonization needs, the project was aligned with the need for a safer operation and a leaner footprint than traditional distillation eliminating the need for additional intermediate tanks, supply pumps, and filters, reducing floor space requirements.
A trusted solution for producing Water-for-Injection
Veolia, having proven success in delivering its Orion systems to an Irish facility owned by the same company, worked with a US-based team to supply an all-electric, membrane-based modular system, compliant with cGMP/FDA – Current Good Manufacturing Practices of the Food and Drug Administration, designed to generate a flow of up to 2.2 gpm (500 liters per hour). The compact, modular system has all its electro-mechanical assembly (i.e. instrumentation, meters, analytical sensing elements, and control valves) contained within skid limits for quick, simple, and low-cost installation on-site.
The pre-treatment of this multi-barrier system includes softeners, and carbon adsorption units for hardness and chlorine removal, respectively. Then, microfiltration removes particles, bacteria, and high molecular weight organics before the water is pressurized by high-efficiency pumps to supply the reverse osmosis (RO) membranes. A hollow-fiber membrane for degassing, along with electrodeionization, and final ultrafiltration are combined to deliver continuous deionized water production while exceeding organics, bacteria, and endotoxin removal requirements to ensure reliable, uninterrupted laboratory operations.
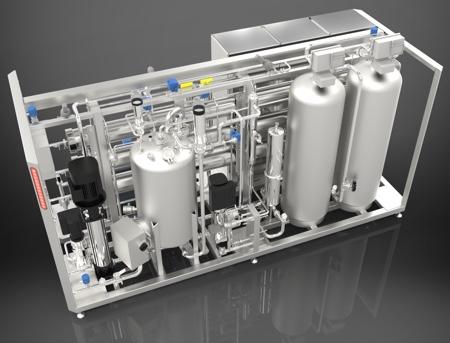
Orion™, which works without the use of chemicals and is fully automated to start hot water sanitization cycles, builds on its 3rd generation of improvements following hundreds of successful installations across healthcare sectors and around the world providing a blueprint for future sustainable upgrades in other facilities.
The system is connected to a control panel with a human-machine interface (HMI) (installed within the boundaries of the packaged equipment skid) and interacts with all logic, instruments, and sensors tracking temperature and conductivity as well as chlorine and hardness levels. During regular operation and sanitization procedures, it is also linked to the building management system (BMS) for control purposes and alarm status along with notifications.
To further advance energy and environmental benefits post-production in the building distribution loop, ozonation is typically preferred in lieu of steam-heated hot water circulation. Operated on a continuous basis, ozone is injected in the storage tank where stagnant waters elevate the risk of bacteriological growth. An ultraviolet (UV) disinfection unit provides ozone destruct capabilities to ensure the depletion of dissolved residual ozone. During sanitization of the loop, UV is switched off to allow for thorough sterilization and protect against bacterial contamination.
Sustainability features of Orion™
Veolia puts resource efficiency at the heart of its Orion™ system avoiding water waste and energy-related emissions. During recirculation, a cooling heat exchanger maintains low temperatures that prevent microbiological growth allowing for this water to be recycled instead of discharged to the drain during recirculation. During service, a second membrane element halves the rejected concentrate stream reducing the water discharged and boosting water recovery by as much as 20% compared to conventional processes.
Solutions to Operational Challenges
Producing cold WFI water with Orion™ makes sense economically and environmentally but can present operational challenges without adequate skilled manpower. To this end, taking full advantage of modern digital tools and maintenance programs can be helpful. Through real-time monitoring and analytics, Veolia’s Hubgrade platform can automatically and instantaneously help operators enhance productivity and compliance while extending the system's lifetime and avoiding costly breakdowns. Best-in-class predictive and preventive maintenance program Aquaservice™ provides continuous system optimization with specialized technicians meaning that limited, plant manpower resources focus on their core capabilities while offloading risk mitigation and responsibilities for ongoing system compliance and system uptime.
The role of water in mAbs production process efficiency and cell productivity
From the discovery through to the manufacturing of mAbs and other therapeutic recombinant proteins, the use of water is pervasive. Culturing cells is invariably tied to water quality. The much-needed improvement in the commercial viability of cell lines and development pipelines requires boosting the quality and productivity of cell lines. To this end, media solvents and reagents free of impurities are key to maximizing protein yield and avoiding the risk of contamination and product loss that can significantly affect throughput.
Transitioning to Cold WFI
Either at an R&D lab or a commercial facility, the production of low-energy WFI to prepare endotoxin-free media and buffer solutions can be an opportunity to turn an environmental liability into a driver of significant utility savings and environmental benefits. Because WFI is often one of the most intensive energy users when produced via steam-heated distillation, replacing it with a membrane-based generator at ambient temperature delivers crucial net-zero gains. When powered by green energy and coupled with ozone sanitization, the solution leads to the convergence of electrification and renewables, the best path to achieving carbon neutrality.
By using membranes to produce WFI instead of boiling it with stills, this project stands as a model for a host of other facilities in need of decarbonizing traditionally steam-driven, carbon-intensive processes, while making them cleaner, leaner, safer, and more profitable, all key attributes to continue building on the industry’s record growth of antibody therapeutics.
Harnessing its market-leading technological expertise, Veolia deploys a comprehensive climate-smart approach to WFI production to transition life sciences and biopharma companies to achieve net-zero carbon across their own operations both in a laboratory and commercial manufacturing scale tackling the twin challenges of electrifying carbon-intensive WFI processes and powering them with renewable sources. This enables not only the discovery and production of innovative medicines but also the rapid decarbonization and achievement of emission reduction targets and climate commitments marking a major contribution towards keeping biopharmaceutical companies at the forefront of innovative immunotherapies against cancer and other conditions in a sustainable and environmentally friendly way.
Need help navigating the best option to produce Water for Injection?
Our experts are able to help you explore the available technologies and evaluate the best option for your facility.