Overcoming challenges in high-purity SOP production utilizing crystallization
As the population increases so does the demand for crops. Unfortunately, some crops are sensitive to chloride, and traditional potassium fertilizers cannot be applied. As a result, high-quality water-soluble fertilizers are being utilized to ensure successful crop yields of these agricultural products, but the production of crystalline fertilizers, especially sulfate of potash (SOP), is a complex endeavor.
From ensuring success through lab feasibility and piloting to creative SOP production, Mark Boone, General Manager from HPD® Evaporation & Crystallization — a Veolia Water Technologies subsidiary — shares his evaporation and crystallization experience to help industries keep up with demand and ensure quality.
Challenge one: managing complexities to ensure performance and control costs
The investment in an evaporation and crystallization process is large and comprehensive feasibility so a testing process should be considered to ensure performance enhancements and to evaluate cost-effective approaches. It’s imperative to perform bench or pilot-scale tests to confirm the design parameters using the actual feed solution expected for the commercial plant or, if not available, a synthetic solution based on the best available knowledge. Pilot capabilities provide a proving ground for each system during project development and identify potentially costly issues prior to commissioning.
Challenge two: creative options for SOP production — upgrading potassium chloride to SOP
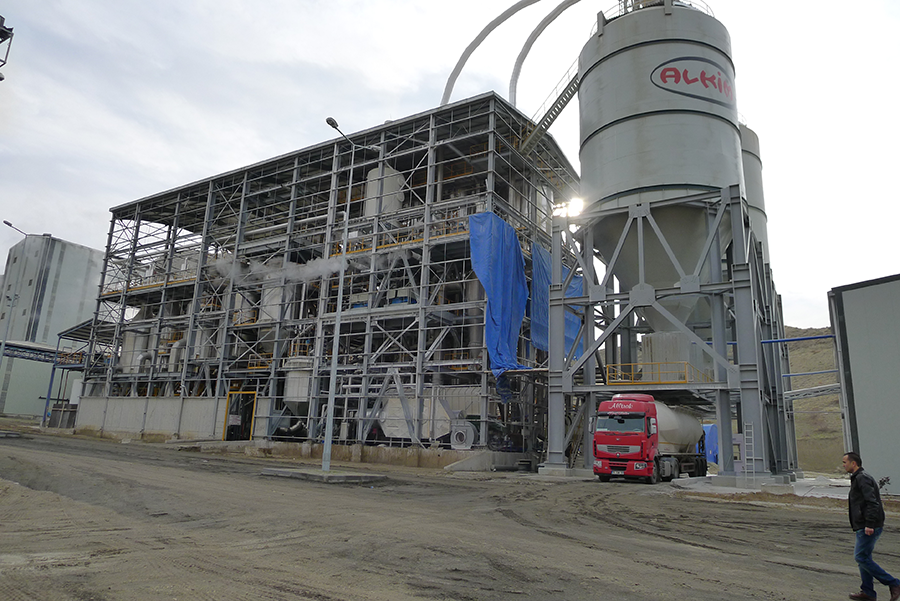
Importing chloride-free fertilizer for crop production can be cost-prohibitive so an option is to make it available locally. For example, Turkish-based Alkim Alkali Kimya A.S. (Alkim), one of the largest sodium sulfate producers in the world, decided to invest in its Koralkim facility to produce up to 50,000 tons per year of soluble-grade SOP. We supplied our HPD® crystallization technology to produce SOP in crystalline, a fully soluble form. The multi-stage chemical reaction between potassium chloride and brine saturated with sulfate salts from Alkim’s existing operation takes place inside draft tube baffle crystallizers that promote the growth of highly pure SOP crystals. This solution, which also includes multiple-effect crystallizers to produce almost 35,000 tons per year of food-grade sodium chloride as a by-product, optimizes capital investment by utilizing Alkim’s existing cogeneration units.
Challenge three: expanding operations
Owing to market demand many of our customers need to expand their existing operations and infrastructure which can be limited in terms of space and the availability of natural resources, such as water, in the area. One such example is the crop nutrient and salt producer, Compass Minerals, who needed to expand SOP production at its plant in the USA. We Integrated an HPD® PIC™ crystallizer unit into the existing plant which converts a brine feed containing schoenite into a high-purity SOP product and is marketed by Compass as Protassium+®. Thanks to more efficient recycling, Compass has been able to significantly reduce water consumption, relative to the existing SOP plant while also providing for a more efficient plant operation.
Challenge four: utilizing other sources of SOP to capitalize on stock
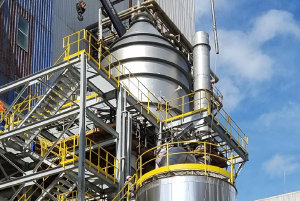
Another option is to manufacture SOP from the waste streams of pulp and paper mills. In this process, glaserite (a double salt of SOP and sodium sulfate) is initially recovered via a black liquor ash treatment system and then converted into high-quality SOP crystals for fertilizer use. Whatever the feedstock option, the crystallization process holds the key when it comes to controlling the purity and size of the final SOP crystals. At a pulping manufacturing facility in Brazil, the pulping production uses a washing process to increase the purity of the pulp. The resulting product is a liquid stream that is rich in organics for energy production. This liquor, however, requires the removal of chemicals to avoid the undesired build-up of chloride and potassium in the recovery cycle, which if left uncontrolled, can create corrosion and boiler fouling. To prevent this fouling and corrosion, 650 tons per day of precipitator ash from the boiler is treated using the Enhanced Chloride Removal Process (ECRP™) crystallization technology. The ECRP technology allows for the removal of impurities while taking a previous waste product and utilizing it to fertilize the next crop of trees for pulp production.
Challenge five: meeting future SOP demand
As the economy continues to become more circular and companies look to minimize waste and invest in sustainable processes, there will be more opportunities that provide a win for both the bottom line and society. Forward-looking producers can now seize higher-margin opportunities in the fast-growing agricultural market by producing specialty products utilizing previously unexploited feedstocks both profitably and sustainably by incorporating innovative processes.