What is Water for Injection?
Water for Injection (WFI) is sterile water used for the manufacturing of pharmaceutical products which are administered parenterally, ophthalmically, or inhaled. WFI also is used for cell culture growth media, washing, and rinsing bioreactors in fast-growing biologic therapies.
Water for Injection is similar to purified water; it must meet the same quality requirements as this water purity classification but needs to undergo additional treatment to meet the strict endotoxin limits to be considered safe for injection.
Systems producing WFI also need to undergo a validation process to ensure it is producing water that meets the required specifications in order to be used safely.
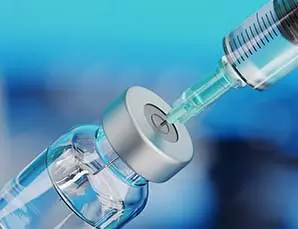
Browse these Helpful Water for Injection Resources
Water for Injection Specifications
To be an acceptable source of WFI, the USP (US Pharmacopeia) and the European Pharmacopeia require that water produced using distillation or membranes must meet strict specifications for conductivity, bacteria, TOC (total organic carbon), and endotoxins. (See the chart below for WFI specifications).
Water for Injection Quality Requirements
USP (US Pharmacopiea) |
European Pharmacopoeia |
Japanese Pharmacopoeia | |
---|---|---|---|
Conductivity |
< 1.3 μS/cm at 25°C* |
< 1.1 μS/cm at 20°C |
< 2.1 μS/cm at 25°C** |
Bacteria |
<10 cfu / 100 ml (Guideline action limit) |
<10 cfu / 100 ml (Guideline action limit) |
<10 cfu / 100 ml (Guideline action limit) |
TOC |
< 500 ppb |
< 0.5 mg/l*** |
< 0.5 mg/l |
Endotoxin |
< 0.25 l.U. / ml |
< 0.25 l.U. / ml | < 0.25 l.U. / ml |
* Offline conductivity measurements possible. If in-line conductivity exceeds values then refer to USP tables in section 645 **Offline conductivity limit after agitating ***or pass oxidizable substances test |
Two Methods to Produce Water for Injection
1) Membrane systems (Cold WFI)
Cold WFI production methods include reverse osmosis combined with a secondary membrane such as ultrafiltration. Compared to distillers, membrane systems often have lower costs and take up less space. The drawbacks are greater contamination risks and monitoring needs due to ambient (“cold”) operating temperatures, but these can be mitigated with periodic hot water sanitization. For several decades, cold water for injection has been permitted by the USP (United States Pharmacopeia) and the Japanese Pharmacopeia (JP). In 2017, the European Pharmacopeia (EP) was the last of the three major pharmacopeias to approve membranes for the production of water for injection. This approval states water for injection can be produced through "reverse osmosis, which may be single-pass or double-pass, coupled with other appropriate techniques such as electro-deionization, ultrafiltration or nanofiltration."
The system must also adhere to the following:
- Contains no added substance
- Must be designed to prevent microbial contamination and formation of microbial endotoxins
- Must be validated
- Correct maintenance of the WFI production unit is essential
Since the European Pharmacopeia (EP) made this regulatory change, it has allowed pharmaceutical companies to have a cost-effective, highly reliable alternative to distillation.
2) Distillation (Hot WFI)
This traditional hot process involves a phase change of water into steam to remove bacteria and endotoxins, before condensing the steam back into liquid. High operating temperatures ensure optimal water purification with low contamination risks. On the other hand, there are significant downsides like high energy costs and large system footprints.
What are the advantages of Cold WFI?
What are the advantages of Cold WFI?
There are several advantages to installing a membrane-based system for the production of water for injection when compared to distillation:
- Lower CAPEX equipment
- Reduced engineering costs from less complex system design
- Lower life-cycle cost (labor, operations, etc.)
- Lower energy costs (thermal)
- Increased sustainability (low carbon footprint)
- Smaller actual footprint from the elimination of distillation equipment
- Can be hot water sanitized to eliminate biofilm risks
- Increased safety (no need for steam generation)
What are the advantages of distillation?
What are the advantages of Distillation?
- Effective purification of sanitized water
- Low risk of endotoxins from high operating temperatures
- Used for several decades for WFI production
How to select what type of system is best to produce WFI
How to select what type of system is best to produce Water for Injection
Customers have a choice when selecting what type of system to produce water for injection. The factors that go into a decision on the process and system are numerous. Both Cold WFI systems and Hot WFI systems will produce water that will meet the specifications for "water for injection," the decision will depend on factors such as the operational requirements, existing equipment and systems, available space, budget and the previous clean water utility experience of those in the organization.
Another important factor that is being reviewed when evaluating either Cold WFI or Hot WFI systems is sustainability and carbon footprint. The amount of energy needed for these processes varies greatly and can be an important element in helping companies obtain their corporate environmental and sustainability goals.
What type of system is the most sustainable?
What type of system is the most sustainable?
Cold WFI (membrane-based systems) can be an integral part of helping pharmaceutical companies significantly reduce their carbon footprint. Distillation requires large amounts of carbon-intensive energy, mainly in the form of steam, to produce high purity water to be used in the manufacturing or distribution of pharmaceutical products.
Membrane-based systems are now an approved and accepted process to produce water for injection. Because Cold WFI systems operate at room temperature and require less energy, they inherently have a smaller carbon footprint. Furthermore, as traditional electric grids continue to move away from fossil fuels to less carbon-intensive energy sources, the carbon footprint of these systems will hopefully continue to decline over the life cycle of the system.
Need help navigating the best option to produce Water for Injection?
Our experts are able to help you explore the available technologies and evaluate the best option for your facility.