What is degassing water?
Degassed water or water degasification is the removal or reduction of dissolved oxygen, carbon dioxide, and other gasses from water.
What are some of the various degasification techniques available?
Some of the various degasification methods include:
Vacuum Degasification
Vacuum deaerators, also known as vacuum degasifiers, use a vertical pressure vessel, multiple vacuum stages and vacuum pumps to continuously remove objectionable gases from liquids
Thermal Degasification
Thermal degasification applies steam heat to remove gasses from a water stream via boiling. It is a physical process that consists of removing the dissolved gases by taking advantage of their insolubility at high temperatures
Membrane Degasification
Membrane degasifiers use a hydrophobic gas permeable membrane to remove dissolved gasses such as oxygen or carbon dioxide from a liquid stream, transferring the gas into a stripping gas or vacuum stream
Chemical Degasification
Chemical degasification uses the injection of chemicals such as sodium bisulfite, hydrazine, or amines to remove dissolved gases from a liquid stream via a chemical reaction
Absorption-based Degasification
Absorption-based degasification uses a counter-current stripping gas stream to absorb a dissolved gas, removing it from the liquid stream and transferring it to the stripping gas stream. Examples are:
- Packed tower strippers: highest efficiency but prone to fouling
- Sieve tray tower strippers: next highest efficiency; also prone to fouling
- Microbubble strippers (CoStrip): highest fouling resistance
Steam Stripping Degasification
Steam stripping degasification uses high-pressure steam injected at the bottom of a stripping column to remove volatile organic compounds or dissolved gases, such as ammonia, from a liquid stream
Veolia is an expert in vacuum deaerators, pressure leaf filtration and degassing techniques.
Vacuum Degassing Method
Vacuum deaerators, also known as vacuum degasifiers, is a water degassing system that uses a vertical pressure vessel, multiple vacuum stages and vacuum pumps to continuously remove objectionable gases from liquids. Packed towers, supported by powerful vacuum pumps, reduce the surrounding vapor partial pressure which promotes the mass transfer from the liquid to the gas phase. Veolia’s proprietary system design provides the best value in the market by optimizing the tower diameter, number of stages, packed bed geometry and vacuum capacity on the basis of the salinity, temperature, and other conditions of the influent water.
Main Features of Vacuum Deaerators
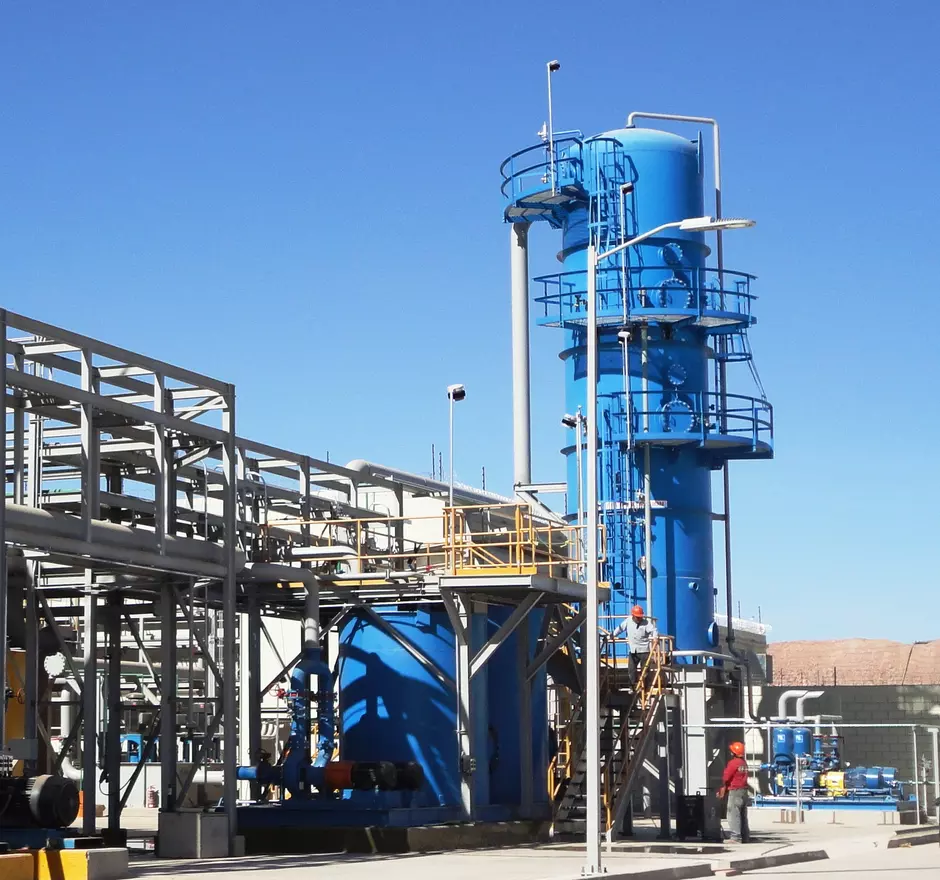
A vacuum deaerator system consists of the tower with integral catch basin, vacuum pump and forwarding pump. Demisters and condensers on the vacuum lines are employed to protect the vacuum pumps from corrosion and damage by moisture entrained in the gas stream. Water seals are an integral design of the forwarding pumps to prevent the re-introduction of air into the water. Finally, level transmitters are utilized to control the feedwater flow rate, prevent flooding and protect the forwarding pumps from cavitation.
Veolia can provide a stand-alone solution degassers with capacities ranging from 100 to 10,000 gpm for a single degassing unit, or complete systems that can include additional vacuum towers, liquid ring vacuum pumps, ejectors, mass transfer packing, chemical oxygen scavenger dosing skids and transfer pumps. Veolia selects materials of construction to provide effective surface corrosion resistance under the most aggressive service conditions.
Operation
In vacuum degasification, uniform feed-water distribution and downflow hydraulic balancing from the top of the tower and over its cross section is a key design consideration as the water flows through a bed of mass transfer packing that maximizes the liquid/vapor-phase contact area and, thus, reduces residence time and lowers vacuum requirements. As the vacuum degassing system withdraws all the gasses from the vapor phase, it reduces the system pressure below atmospheric pressure which promotes the dissolved gas molecules in the water to diffuse into the vapor phase. Thus, the concentration of gas in the water is reduced. Under this condition, the dissolved gasses in the liquid are extracted and evacuated from the top of the tower. The intensity of the vacuum and the volume of vapor removed from the system determine the degree of removal.
For some applications of degassing water where extremely low levels of dissolved gases are required, two-stage towers are designed to optimize the extraction process by phasing the removal process with increasingly higher degrees of vacuum. These systems employ a taller tower that has two independent beds of random packing with dedicated vacuum pumps for each bed. The two-stage vacuum deaerators have specially designed internals to ensure high-efficiency gas removal without flooding or short-circuiting. An effective pressure sealing method between these two stages guarantees the pressure differential between them. This feature in the design achieves the removal of gases more efficiently than in a single-stage step processes which would require a much larger vacuum capacity.
The last traces of dissolved gases are the most difficult to remove and the concentration can never be reduced to zero. Generally, 50 parts per billion (ppb) of oxygen is the lowest practical level that can be achieved with vacuum degasification. After the second-stage packing, the liquid is allowed to settle in a sump section to allow for the applied sulfite-based oxygen scavenger chemical to react and help reduce the residual oxygen concentration even further, if required. The sump or storage section, located at the bottom of the tower, collects the de-gasified water and provides the net positive suction head requirements (NPSHR) of the forwarding pump.
Markets and Applications
Vacuum deaerators are used primarily on water streams to remove dissolved gas content gases including oxygen, nitrogen, carbon dioxide and volatile organics that can produce corrosion, scaling and plugging of piping and injection systems. When used in boiler feedwater treatment systems, they provide a cost-effective means of removing carbon dioxide between cation and anion exchange columns. Veolia’s vacuum degasification systems are also commonly used to remove oxygen as part of the Merrill Crowe process in gold and silver mining. Other degassing water applications include oxygen removal for corrosion protection in enhanced oil recovery using seawater, as well as Process Water Oxygen Removal in the Power industry.
Before produced water can be reused, recycled, or further treated, a complex mix of undesired dissolved gases and other contaminants must be removed. However, removal of these dissolved gases can be extremely challenging.
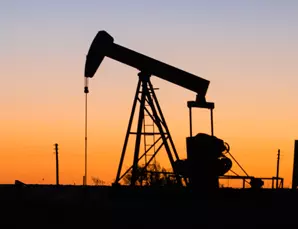
Produced water can contain high amounts of oil and suspended solids that can lead to difficulties for conventional methods of gas removal such as packed or sieve tray towers. Significant contamination by suspended solids or oils can result in plugging or fouling of the tower internals. This means that to remove hazardous or undesirable gases, many pretreatment steps must be added ahead of the tower. In applications where produced water contains high levels of suspended solids and oil, conventional approaches tend to fail quickly and, as a result, alternative technologies are emerging that can be more effective at removing dissolved gases, even in highly contaminated wastewater streams.
A novel gas stripping technology
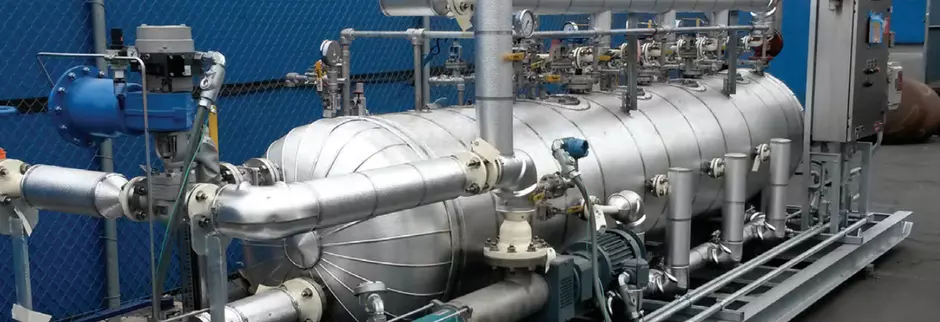
Developed by Veolia Water Technologies under the name CoStrip, this novel degasifier uses a series of separation cells and a stripping gas stream such as air, nitrogen or fuel gas. The stripping gas runs in the opposite direction to the bulk fluid flow across a horizontal vessel. Raw water is introduced at one end, flows through the vessel and the effluent exits at the other end. The horizontal design makes it an ideal solution for installations with height restrictions.
Each separation cell is equipped with an eductor where the stripping gas is introduced as microbubbles at the bottom of the vessel. The small size of the microbubbles provides the surface area needed for the gas-liquid interface, as well as increases the retention time for the bubbles to rise allowing for adequate contact time needed for mass transfer.
The dissolved gases present in the bulk liquid, such as H2S, CO2 and BTEX, migrate into these bubbles as they rise, a process which is driven by the disequilibrium between the dissolved gases present in the bulk phase and within each tiny bubble. Once these bubbles reach the liquid-gas interface, they pop and release the absorbed gases into the headspace, where they can be removed for further treatment or disposal. Continuous gas sweeping in the headspace and the introduction of fresh stripping gas into the bottom of the vessel provides the constant gas disequilibrium needed for optimal gas stripping.
Proven performance for gas stripping
Veolia Water Technologies’ CoStrip degasification unit has been shown to effectively remove gases such as CO2, H2S and BTEX compounds even in very challenging produced water applications. Where the use of a packed tower or sieve tray towers is not an option due to high levels of suspended solids and oil, this new technology is able to meet required effluent water quality. It has been proven to remove VOCs like benzene, toluene and ethylbenzene as well as acid gases. Performance validation field demonstrations concluded that CoStrip removed 85% of BTEX compounds, 77% of the CO2 and 85% of H2S gas present in the raw water meeting the target removal for BTEX. Performance can be adjusted to meet the removal percentage of any target contaminant.
In addition to its significant performance advantages, using CoStrip to remove CO2 upstream of a chemical softening step also reduces the requirement for water softening chemicals as well as sludge. The CoStrip process removes excess alkalinity associated with carbonates and bicarbonates present in the water. Typically, any excessive alkalinity needs to be removed to prevent scaling of downstream processes. The CoStrip technology therefore reduces the demand for hydrated lime and caustic soda that would be required, resulting in significant cost savings and reduction of the calcium carbonate and magnesium hydroxide sludge generated.
CoStrip technology eliminates the need for upstream treatment before degasification reducing CAPEX and OPEX cost and can be used as a pre-treatment step to reduce corrosion associated with acid gases. By removing acid gases like H2S, there is no need to cover downstream process tanks, which would otherwise be necessary to prevent odor emissions and ensure the safety of personnel. Operating costs are reduced by eliminating the need for oxidants to remove H2S, improving equipment longevity and performance. In addition, where a treatment train includes a Reverse Osmosis (RO) system, it has been found that removing volatile organic compounds will extend the life of the RO membranes.
Although any assessment is case-specific, the estimated economic benefits of using the CoStrip technology include up to a 30% cost reduction on chemical softening and sludge disposal and up to 35% cost savings on reverse osmosis membrane replacement. These figures suggest a payback period of less than a year when gas stripping technology is added to a water treatment process train. While reduced capital and operating costs are clearly beneficial, by removing CO2, H2S and various VOCs, CoStrip allows facilities to ensure personnel and equipment safety, meet stringent effluent water discharge and air quality limits and the most stringent regulatory demands in even the most challenging produced water applications.
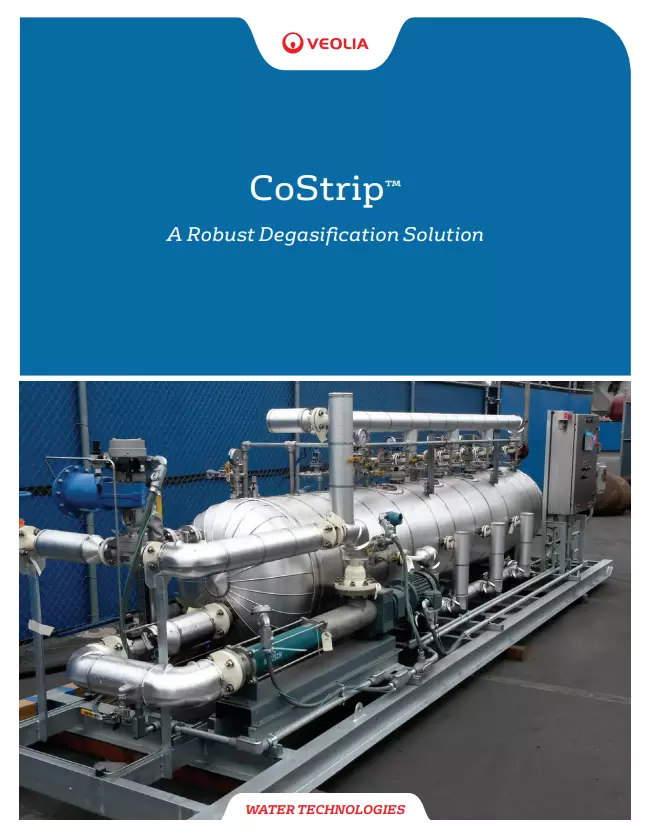