E&P Feels the Heat: How Thermal Solutions Can Solve Hot Water Issues
Matias Navarro and Mark Nicholson, Veolia Water Technologies – North America, show how responsible reuse and recycling will be a major factor for continued growth and future profitability for oil and gas producers, even within a persistent market downturn.
Energy exploration and production (E&P) activity has been depressed over the past 5 years since the slump in oil prices in 2014. Despite trade tensions and concerns around the health of the global economy, production from unconventional fields, such as shale or oilsands, has become increasingly efficient and cost-competitive. However, this wave of productivity growth seems to have lost sight of one of the most significant operational issues: the management of water. Given that the entire water management process is intensive, complex, and often expensive, it is hard to explain why water is not at the top of oil producers’ minds. However, not acknowledging water management issues such as utilization of freshwater sources to disposal of large volumes of produced water will dampen future growth in the oil patch. Water management is a major challenge which can present serious risks to not only the producers’ growth and profitability, but also their environmental reputation.
Despite the sustained market downturn and limited access to raise cash, some forward-looking producers have been seeking additional ways to become more
competitive and cost-effective. One cost-saving tactic is the implementation of water recycling programs that enable growth and unlock efficiencies, while also boosting the social value and environmental profile of unconventional oil and gas production.
Unconventional challenges
Over the past few years, oil and gas E&P activity has boomed in North America, but not without generating growing headaches for many producers. To begin with, sourcing water is becoming more problematic. The amount of water withdrawals as a percentage of the total water available is forecast to rise substantially by 2025 amid intensifying competition between irrigation, farming, and other industrial uses. At the same time, despite heavy rains in some parts of the world, water shortages have been more frequent in energy-rich areas such as western Texas, US. Long distances to water sources, regulation around water withdrawals and public scrutiny heighten the water constraints on producers.
However, a more pressing and often overlooked issue is that of ‘produced water’. Burgeoning production from unconventional sources, coupled with prolonged operations from conventional but mature oilfields has created rising volumes of the inevitable byproduct of oil and gas extraction: water.
Produced water has less than ideal qualities. It is not only up to 10 times saltier than seawater, but is also contaminated with bacteria, suspended solids and toxic chemicals which require removal before disposal or beneficial reuse. The volumes of produced water are staggering. It is estimated that for every barrel of oil and gas produced, 4 – 5 bbl of produced water are pumped to become the energy industry’s largest liquid waste stream. In many cases, this produced water is considered ‘waste’ and is sent directly to disposal wells without consideration for reuse or recycling for other applications.
Meanwhile, to the dismay of producers, the volume of water required for hydraulic fracturing is expected to continue to increase on the back of advances in drilling techniques, with longer wells necessary to stimulate harder-to-reach reservoirs in search of higher yields. Water cuts or water-to-oil ratios can be as high as 15:1 in western Texas.
Although horizontal drilling, fracturing, and pressure-maintaining flooding techniques absorb some excess water, this consumption is only a fraction of what is produced. As water volumes reach the highest level ever recorded, disposal wells reach capacity and brine hauling turns into a considerable logistical expense. As a result, the injection of liquid waste in distant saltwater disposal wells may become a more questionable practice.
While disposing of water through reinjection is the most cost-effective option today, there are powerful economic forces driving a transition to more localized water management in the long term. Amid concerns about contamination of drinking water sources and seismic activity around disposal wells, regulations and geological limitations prevent operators from disposing of water in wells in close proximity to drilling operations. Furthermore, as the distance to haul this water
off-site increases, trucking becomes more expensive. Logistics costs are especially high in areas with tight labor markets and less-developed transfer systems. Thus, disposal becomes more costly from both an economic and environmental perspective.
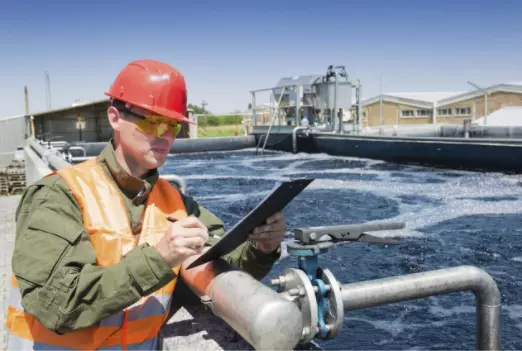
E&P activity has boomed in North America, but sourcing water to fuel this boom is becoming more of an issue. Producers compete with farming and other industries for water, experience logistical issues to water sources, plus some plays are seeing lower rain yields.
Dealing with tough waters
Given that water-related expenses represent approximately 50% of E&P operating costs, controlling water management spending is a crucial step for producers in a low oil price environment. To this end, the implementation of water recycling technologies solves the need to reduce both freshwater withdrawals and produced water disposal. With increased adoption and improved economics, it is expected that recycling and reuse programs will double their share of the water management market from 10 – 20% in the next 5 years. However, water reuse will only rise up to the need to meet frac water demand. Because hydraulic fracturing produces up to five times more water than needed for reuse, the recycling of water outside the fence is an opportunity to reduce risk and create value for industries, farmers, and communities.
At first, water reuse involves relatively inexpensive treatment technologies to target the removal of particulates such as fine solids and bacteria, but also that of organics such as dispersed oil. Both are typically removed by filtration, flotation, or membrane separation. Further downstream, scale formers such as iron, barium, strontium, or calcium are often removed by chemical precipitation or ion-exchange softening, a technique that selectively replaces hardness ions. The last barrier to recycling produced water beyond the limits of oilfield needs lies in the reduction or removal of dissolved solids.
Due to their major importance in the overall investment, desalination technologies require a careful analysis of the upfront CAPEX and OPEX necessary to keep the plant running once it is online. OPEX typically includes the labor, operational replacement parts, and disposal of waste streams.
Desalination processes used for recycling, either based on the use of heat or the application of membranes, are viable solutions.
Both technologies can be capital-intensive compared to reuse only technologies. The high salinity of produced waters from most unconventional plays and the challenging operating environment of oil and gas installations requires materials that are chemically-durable, corrosion-resistant, and suitable for elevated temperatures for the economic life of the facility (usually 15 – 25 years).
Membrane systems have lower operating costs and often lower capital costs. The capital tradeoff is the pretreatment step required to protect the membranes and avoid fouling and subsequent chemical cleaning which impacts performance and operation. Often these pretreatment steps can involve multiple unit operations and can significantly increase the membrane capital cost; the CAPEX of a membrane system can equal that of a thermal system.
Conversely, centralized plants using evaporative systems such as advanced brine concentrators and crystallizers are more energy-intensive. However, they are also more robust and reliable, as they can be used on any kind of high-salinity feed water and can deliver higher water recoveries vs membranes, including zero liquid discharge if necessary.
Although thermal technologies have higher capital and operating costs, large-scale treatment needs can be made more economical because of the efficiencies in heat recovery which reduce energy costs. In doing so, evaporative systems are categorized into two types depending on the way they handle the vapors generated. Highly efficient mechanically-driven systems re-compress vapor, using it to drive additional evaporation by electrical means. In contrast, thermal-driven systems use high pressure steam to recycle vapor and drive additional evaporation. This is normally done in multi-effect mode where the vapor created in one evaporator is used to drive additional evaporation in the next ‘effect’. Thus the amount of source steam can be reduced by adding ‘effects’. Due to evolving compression technology, next-generation systems will achieve further reductions in energy costs and emissions.
Ultimately, the efficiency of both membrane-based and thermal-based solutions is limited by osmotic pressure and thermodynamics, as the need for increased amounts of energy results in diminishing returns to remove water from a brine with rising salt concentration.
However in the context of increasing logistical challenges, thermal concentration systems can concentrate brine higher and thus produce a lower volume of a heavy saturated brine. The follow-on is minimal transportation and disposal costs. Implemented through either mechanical recompression or multi-stage evaporation, thermal systems often achieve 70 – 90% water recovery. When crystallizers are incorporated to concentrate solutions beyond salt saturation levels, the operation precipitates dry solids reaching zero liquid discharge, with water recoveries nearing 100%.
Equally, if freshwater sourcing is limited and waste minimization is not as important as delivering a water stream of suitable quality for reuse, then a membrane technology with lower recoveries may be more appropriate.
Hybrid alternatives are often evaluated to integrate membrane-based solutions followed by thermal evaporation and crystallizations. This system capitalizes on the ability of membranes to reduce produced water volume at a lower cost, while decreasing the size of thermal concentration systems downstream.
Unfortunately, one size does not fit all. There is no ‘silver bullet’ that solves all of these complicated water issues at once. Each application is different with respect to composition of produced water, volume of produced water generated, amount of water which can be re-used in the oil recovery process, freshwater availability, and disposal logistics, cost, and risk. While no single technology or water management approach can fit all the different treatment challenges across different areas, the status quo around disposal is unsustainable in the face of rising costs and risks for containment, storage, and transportation. Thoughtful water management programs will likely include water disposal and reinjection, as well as longer-term midstream transfer infrastructure to centralized treatment facilities, perhaps using a blend of physical, chemical and thermal methods.
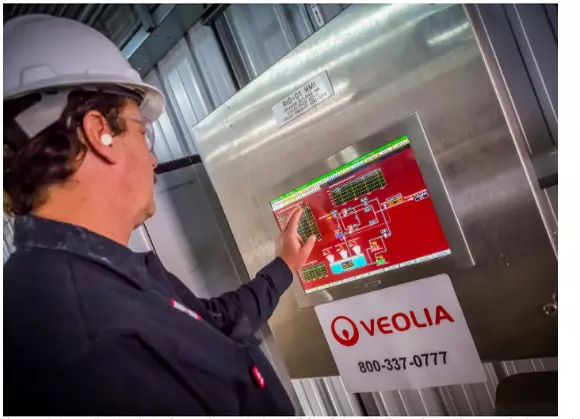
Desalination technologies require careful analysis of upfront costs, between CAPEX and OPEX. The company can assist in gathering information and reviewing cost-analyses.
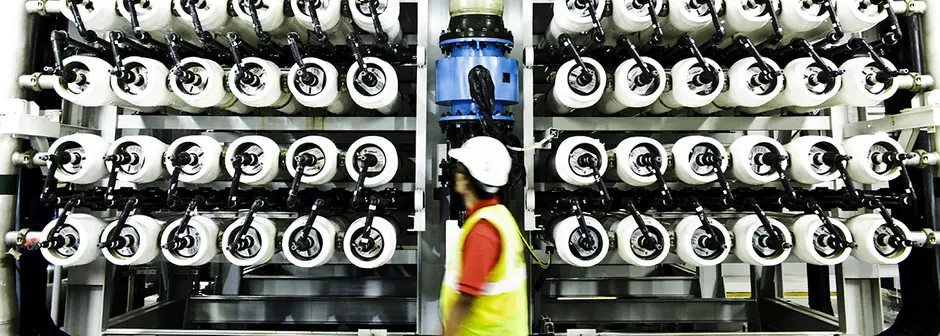
Membrane technologies can offer lower OPEX and energy costs than thermal technologies, but these solutions require pretreatment and chemical cleaning.
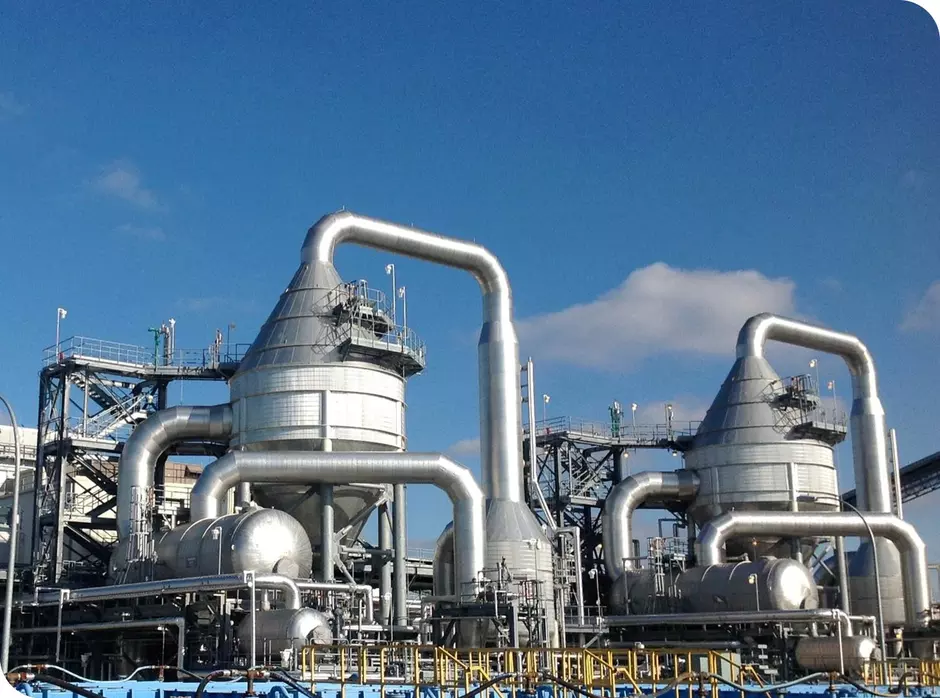
Thermal solutions, such as the one pictured, help large producers achieve better economies of scale for water treatment needs. Implemented through multi-stage evaporation, thermal systems often achieve 80 – 90% water recovery. However, when crystallizers are incorporated to concentrate solutions beyond salt saturation levels, the operation precipitates dry solids reaching zero-liquid discharge, with water recoveries topping nearly 100%.
Juggling act
Oilfield water management is a delicate operation, one that needs careful consideration of operational risks and economic performance. Achieving a balance between short-term needs and long-term goals is not an easy task. However, oil and gas producers must also prepare for the future, which is likely to see a shift toward cheaper and cleaner energy sources. To face this outlook, the management of water through recycling technology will help exploration companies to not only become more resilient but also more competitive, regardless of the market environment.
Producers have made remarkable achievements since the beginning of the shale energy revolution. As the industry matures with stronger players, they must continue this wave of innovation to secure a future with more predictability. Only those players that can lower freshwater usage and costs through better management and technologies will be better positioned to compete, as water sourcing and disposal becomes the limiting factor to growth and stakeholders’ acceptance. Advanced thermal technologies for water recycling are a significant investment. The cost of doing nothing can be much higher.
Originally published in Oilfield Technology January / February 2020