The Challenge
Chemical processing plants such as this one require both heating and cooling capabilities to start and control chemical reactions. As a result, they utilize boiler/steam systems for heating and cooling towers and heat exchangers for cooling. To help them manage their water systems, they will use a water treatment chemical company.
Prior to Veolia’s involvement, the plant experienced uncontrolled microbiological growths in their Ketene Cooling Tower. Slime and algae formed on cooling tower fill, in the basin and on heat transfer surfaces causing inadequate cooling as measured by high approach temperatures. At the time the plant was utilizing chlorine bleach for micro biocontrol, but with some process contamination, it was unable to keep the system under control. Veolia was brought in to solve the problem.
The Solution
Often, when chlorine is unable to provide adequate bacteria and algae control, chlorine dioxide is used in cooling water systems. While it can be quite effective, it requires a special feed system that must be purchased or leased, and the chemicals required can be expensive if usage is high. The combination of both was going to cost the plant an additional $30,000 per year.
The technical team at Veolia was contacted for alternatives and based on system conditions and issues, Hydrex 2252, a bio-dispersant, was recommended to be utilized along with the chlorine bleach. It was felt that this would be the most cost-effective solution for both an on line clean-up and ongoing maintenance program.
Process Description
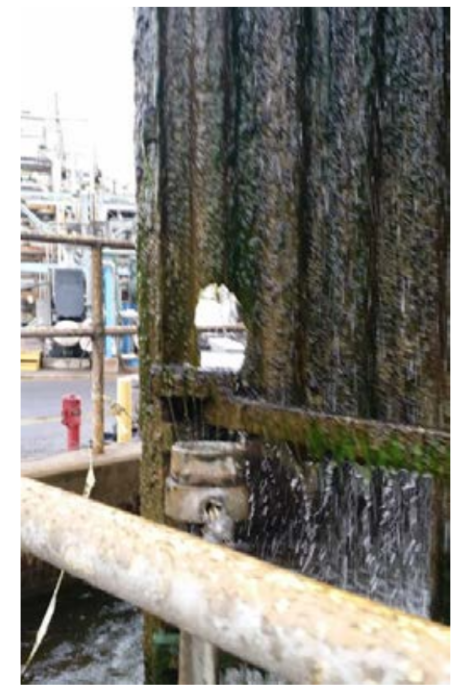
The Celanese, Narrows, Virginia plant was built in 1939 and utilizes wood pulp and other chemicals, going through several processes to make cellulose acetate, used in cigarette and air filters. The Ketene unit manufactures an intermediate for the process and has a cooling tower to service numerous heat exchangers. Having adequate, efficient cooling is critical in the production process, and any fouling of the tower or heat exchangers could potentially limit production and have a negative impact on plant output and profitability.
In any water-to-process heat exchanger, there exists a potential for leaks, which will typically result in contamination of the cooling water, in this case with various organic chemicals. There is also potential for airborne contamination from vapors, such as ammonia. A cooling tower makes an excellent environment for algae and bacteria to grow if there is a food source such as an organic or nitrogen compound. Those also will create a demand for the primary biocide, chlorine. While one might think to simply feed more chlorine, we have found that heavy chlorination can cause a number of problems including high costs and corrosion of iron, copper and even stainless steel. In some systems, it has been found to attack cooling tower wood structures. In order to utilize chlorine at a reasonable level, Veolia has developed a product Hydrex 2252, a bio-dispersant, to help the chlorine work more effectively. It allows us to clean up existing biological deposits, resulting in clean heat exchange surfaces, and to maintain them in that condition.
The Results
When Veolia brought in the Hydrex 2252, the tower looked like the preceding picture and heat exchanger approach temperatures were around 12 degrees F. The product was fed continuously at 75 ppm during the clean-up phase. Visually, the water clarity improved and the slime build-up on the tower gradually cleaned up, with no issues of plugging heat exchangers or screens. Approach temperatures dropped in half to 4-6 degrees F, indicating that heat exchange equipment cleaned up as well. Dosage was then reduced to 25 ppm, and the system has remained clean ever since.
Performance You Can See!
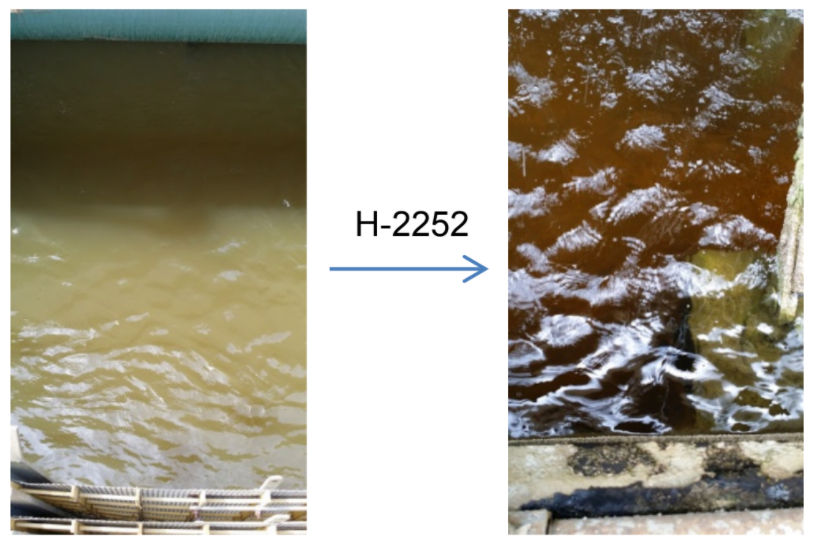
Previously the water was cloudy, indicating high levels of algae, bacteria, and biological debris. Water in this condition makes it difficult for chlorine to do its job to prevent slime deposits in the system.
After Hydrex 2252, the clean water indicates low microbial activity, allowing the chlorine and Hydrex 2252 to keep the system clean, and the plant running efficiently, saving money in both chemicals and production!
The Client
Celanese is a global technology and specialty materials company that has over 26 manufacturing facilities in the US, Europe and Asia. In Narrows, Virginia, they own and operate a cellulose acetate plant, manufacturing fiber-based products.